subsea innovation
UH team partners with Chevron, Oceaneering for remote-operated pipeline inspector
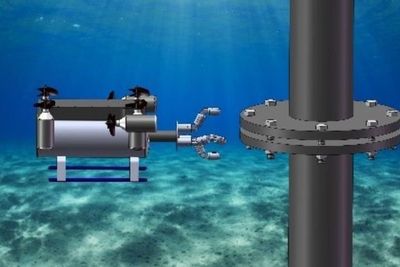
The robots, developed by UH researchers, will provide a safer and more cost effective alternative to pipeline inspections, which are traditionally performed by human divers and require a great deal of time and money. Photo via UH.edu
Two professors at the University of Houston have developed an autonomous subsea vehicle that aims to decrease the number and severity of oil spills.
Known as SmartTouch technology, the Remote Operated Vehicles (ROVs) use smart touch sensors, video cameras and scanning sonars to inspect flange bolts in subsea pipelines, which are considered to lead to increased rates of leakage, according to a release from the university.
The ROVs, developed by UH's Zheng Chen and Gangbing Song, will provide a safer and more cost effective alternative to pipeline inspections, which are traditionally performed by human divers and require a great deal of time and money.
“By automating the inspection process with this state-of-the art robotic technology, we can dramatically reduce the cost and risk of these important subsea inspections which will lead to safer operations of offshore oil and gas pipelines as less intervention from human divers will be needed,” Chen, the Bill D. Cook Assistant Professor of Mechanical Engineering, said in a statement.
The technology will also be highly accurate in monitoring corrosion, which according to Song, the John and Rebecca Moores Professor of Mechanical Engineering, is responsible for most small leaks in subsea pipelines.
The project is funded by a $960,000 grant from the Bureau of Safety and Environmental Enforcement (BSEE), which is a part of the U.S. Department of the Interior. Chen and Song are also collaborating with Houston-based Oceaneering International on the development of the ROVs, which Oceaneering specializes in. Energy giant Chevron will evaluate the technology’s future commercialization, according to UH, and preliminary studies were funded by the university's Subsea Systems Institute.
Thus far, a prototype of the ROVs has been tested in Chen's lab at UH and in Galveston Bay. Experiments showed the technology's ability to inspect the looseness of subsea bolted connections, like flange bolts.
Chen and Song see other applications for their technology, as well.
"Ultimately, the project will push the boundaries of what can be accomplished by integrating robotics and structural health monitoring technologies," Chen added in the statement. "With proper implementation, the rate of subsea pipeline failure and related accidents will decrease, and subsea operations will be free to expand at a faster rate than before.”
Earlier this summer the UH Subsea Systems Institute and SPRINT Robotics teamed up to develop a robotics training program for the energy industry known as “Robotics in Energy.” The first of a series of two-day courses debuted in May and a subsequent course, Automation & Autonomy, will launch next month. Others are expected to be rolled out in the future as part of the university's Micro-Credentialing Programs in UH Energy.
Additionally Chevron and UH partnered up again last month to announce its inaugural cohort of UH-Chevron Energy Graduate Fellows.