A Houston company has teamed up with a Utah-based sustainable cement alternatives producer to construct eco-friendly homes made from 3D-printed pieces.
HIVE 3D was already revolutionizing the home-builder industry with its lightweight gantry system and mobile robotic arm system to 3D print its homes, but it took a giant leap further with its partnership with Eco Material Technologies.
Together, they are building the world’s first near-zero-carbon, 3D-printed homes. Using Eco Material’s cement mixture called PozzoCEM Vite, which has 92 percent lower emissions than traditional concrete that can set in just a few minutes, they are focusing on providing a sustainable, cost-efficient and affordable housing solution.
“We want our homes to last 1,000 years,” Timothy Lankau, CEO, Hive 3D CEO, tells InnovationMap. “We want archaeologists to dig them up and wonder what they were. I mean, you go to the Parthenon in Rome, and it looks similar today to how it did 2,000 years ago because the materials are so stable.
“Concrete's just a very stable material. It doesn't change over time, and that's also why building with stone and masonry is important for the future. We think it's more sustainable because it's ultimately going to be better in terms of longevity.”
Key collaboration
Eco Material Technologies and HIVE 3D’s collaborative mission began through a mutual desire to develop sustainable and eco-friendly solutions for the construction industry.
“Both companies recognized the pressing need to reduce the environmental impact of traditional construction materials and processes and the need for affordable, high-quality housing,” says Grant Quasha, CEO of Eco Material Technologies. “The partnership between the two companies began when Eco Material Technologies reached out to HIVE 3D to explore the potential of incorporating their eco-friendly materials into 3D printed construction.
“HIVE 3D recognized the opportunity to combine their expertise with sustainable material solutions. The finished product of this collaboration is an eco-friendly construction material that can be 3D printed into various structural elements like walls, floors and columns.”
Proof of concept
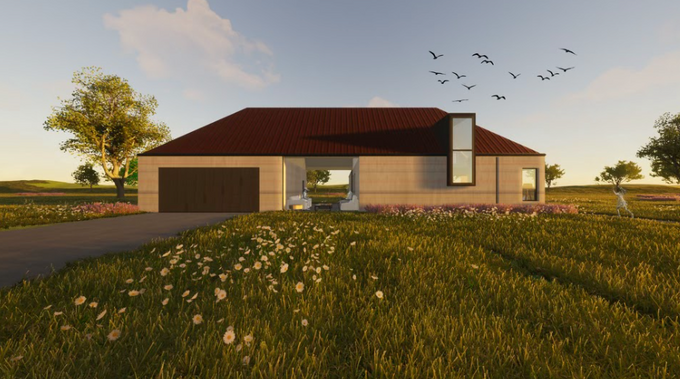
Photo courtesy of HIVE 3D
HIVE 3D’s first full project, a 3,150-square-foot home located in Burton, Texas, was printed with a rotating team of just four people using PozzoSlag, which replaces 50 percent of the portland cement in concrete and has been used in roads and bridges in Texas for over a decade.
The home used several innovations that hadn’t been used in a 3D printed house before, including parametric wall designs, foamcrete wall insulation, and pigmented concrete layers.
“Our product is more sustainable because it utilizes proprietary technology that allows for the use of alternative materials to replace the clinker and processes from traditional cement that contribute to its high emissions,” says Quasha. “It is estimated that the portland cement industry contributes to 8 percent of global emissions annually, but by utilizing Eco Material Technologies' cement replacement solutions ... builders can significantly decrease their carbon emissions without compromising on the product's setting time or long-term strength."
Each ton of portland cement replaced by a ton of Eco Material's products, PozzoSlag or Pozzocem, reduces emissions by close to one ton, Quasha explains.
The Calais project, located in Round Top, Texas, behind the Halles, an antique shopping and design destination, broke ground in March 2023 and will feature a collection of tiny homes known as casitas, including studio, single-bedroom and two-bedroom models, ranging from 400 to 900 square feet.
“These small homes will serve as a model for affordable and eco-friendly housing throughout the country,” says Lankau. “We plan to build them at a speed and cost point that is unprecedented in the affordable housing space.
“Ultimately, we want to build houses at a disruptive price point. We want to be vertically integrated and put our homes on the market at a significant discount to market wherever they are. And by significant, we're talking 20 or 30 percent. That's our goal.”
The right resources
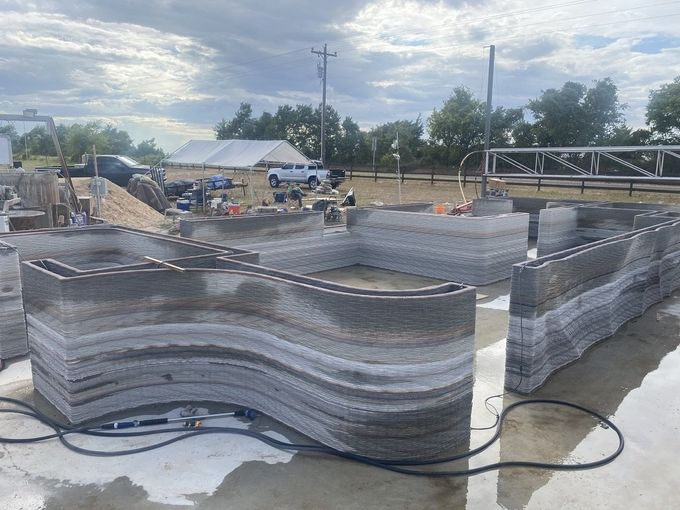
Photo courtesy of HIVE 3D
HIVE 3D worked with CyBe Construction to create a mobile construction 3D printer and mixing system that allows the printing mortar to be mixed onsite, which eliminates a significant amount of labor and time, which means those savings can be passed on to the consumer.
“We worked with a company called CyBe in the Netherlands to build a robotic arm, and that arm has about an 11-foot reach, and it can go all the way in a circle around itself,” says Lankau. “So, it drives around the foundation of the house, printing sections of the house at a time. So, it'll print a section, drive to the next section, and print the next section.
“So instead of having this many different materials and these many different traits, people that do all these different things, we have a machine that just uses one material and prints the wall.”
HIVE 3D has an internal engineer that works through all of the structural issues that may come up on projects and helps them build homes with monolithic, foot-thick concrete walls with rebar and steel supported in them.
According to Lankau, their 3D printed homes are tornado-proof, hurricane-proof, pest-proof, bullet-proof and can virtually withstand anything because of the sustainable materials used to build them.
“They're everything-proof,” says Lankau. “Just because of the natural strength of the concrete and the steel we use to create them, they can support millions of pounds. So, it's actually a stronger material than a typical house. By a factor of 100. Like I said, it's bulletproof and tornado-proof. You could drive a car into it, and it would total the car. I mean, it's a very, very sturdy structure.”
A bright future
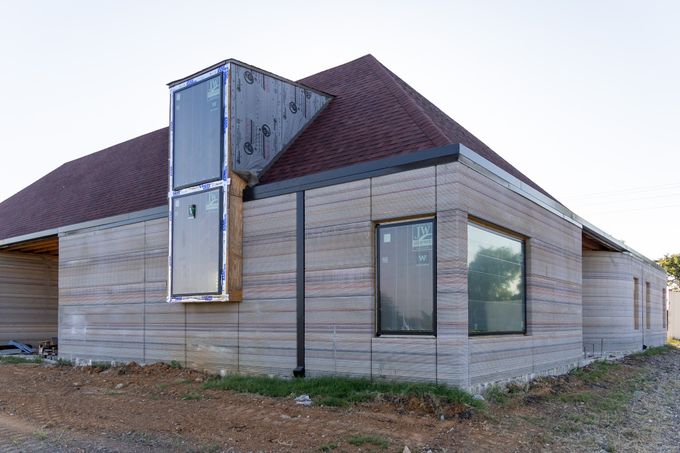
Photo courtesy of HIVE 3D
Moving forward, HIVE 3D would like to continue to innovate and advance its 3D printing technology by leaps and bounds.
“The science fiction goal here, which is maybe a five-year goal, is to be able to drive onto a site, press a button, and watch the robots work,” says Lankau. “We want to be a significant home builder. So, in five years, we want to be building a lot of houses quickly and affordably and we want to continue to automate more and more of the process.”
Right now, there is no formal process for commissioning a HIVE 3D printed home. Perspective customers are directed to the website, then put in a request to build a home, go through a screening process and if the project is a good fit, they'll put that project into their pipeline.
“We can build them quickly. It's just a matter of getting to them,” says Lankau. “We're also going to be doing some developments in Texas probably to start. We also have some international things that we'll be looking into next year. But right now, it's mostly in Texas. We'll be building some developments and putting those homes on the market. We hope to have some out this year and then a bigger chunk next year as we get more machines working. Those will be announced on our website.”
As HIVE 3D continues to find ways to scale its business model, there is a laser focus on the diminishing idea of the “American Dream,” where young families are able to purchase their first home. With the rising costs of supplies and labor, those families have been priced out of the market.
“That’s almost all we think about,” says Lankau. “Homeownership and that part of the American Dream is really struggling right now because the affordability gap between what the average person makes and what the average house on the market costs is just getting wider and wider.
According to Lankau, there are a lot of options to address the supply gap, but there aren’t an equal number of options to solve the affordability issue. Their goal is to find the best ways to deliver real cost savings over both traditional construction and other automated technologies.
“About three weeks ago, we kind of hit the inflection point in our current project where we printed a little house in three days. The cost of the house was what we wanted the cost to be, which is a disruptive amount less than what you could do traditionally or with any other construction technique. And we said, okay, now we're far enough along. We have this system. It's a scalable system. So, we're right now putting some capital together to go out and buy, build more of these machines and get out and start doing these truly affordable housing projects. Because that's where our heart is. Our heart's on the affordable side.”
HIVE 3D’s project in Burton, Texas isn’t available for sell yet, but it will be listed on Airbnb for interested customers to go and experience when it’s completed.
Additionally, the Casitas units in Round Top will be short-term rentals for festival patrons.
“We’ll go directly to market with our next projects,” says Lankau. “And then we'll sell that big house property in Burton at the end of this year.”
------
This article originally ran on InnovationMap.